Latest News: ABCorp 3D Receives ISO 13485 Medical Device Certification. Learn More.
3D Printing Overflow Support During High-Demand Periods
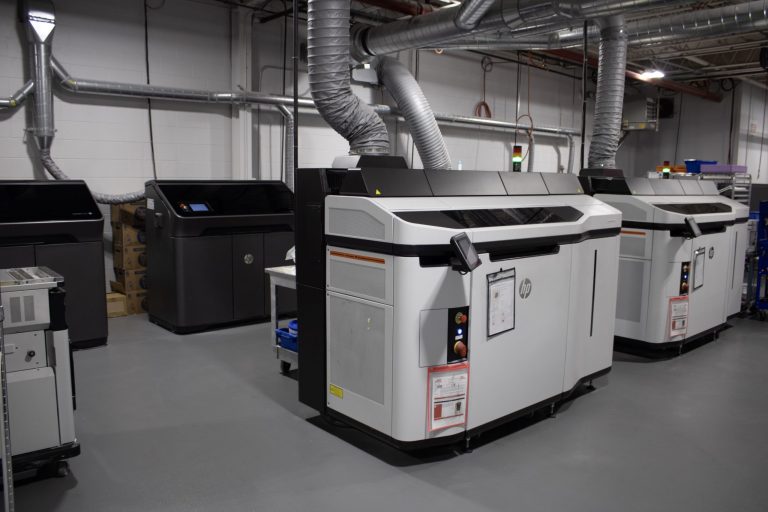
Outsourcing overflow work requires a partner that can be relied upon to maintain the same standards of quality, security, and efficiency that you would expect from your own in-house team. With our expansive material selection, industry-leading security measures, rapid turnaround capabilities, and commitment to personalized service, we are proud to be that partner for many 3D printing businesses.