Latest News: ABCorp 3D Receives ISO 13485 Medical Device Certification. Learn More.
Lean Manufacturing with Additive Manufacturing
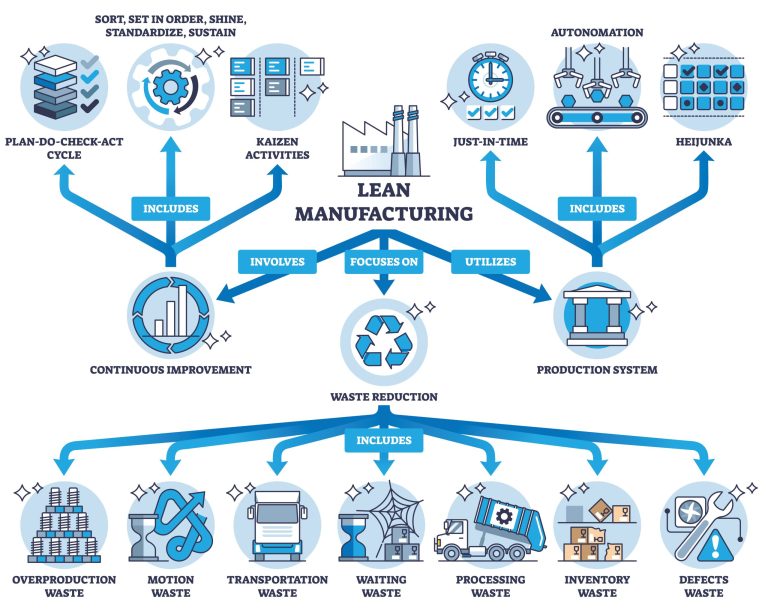
Discover how 3D printing embodies the lean manufacturing philosophy, streamlining production, reducing waste, and enhancing flexibility in industries like medical and automotive. Explore the synergy between additive manufacturing and lean principles to maximize efficiency, minimize costs, and elevate customer satisfaction.